Nem sempre os dissipadores de calor são olhados com o devido cuidado nos projetos que envolvem dispositivos de potência e mesmo aqueles que, aparentemente, não geram uma quantidade preocupante de calor.
No entanto, os problemas relacionados com a dissipação de calor são muito mais importantes do que muitos pensam, e por não estarem relacionados com o circuito em si, nem sempre são devidamente tratados pelos desenvolvedores.
Neste item de nosso curso trataremos deste assunto, focalizando alguns pontos importantes que envolvem o modo de operação dos dissipadores de calor, a forma mais comum de se manter a temperatura de um componente sob controle.
Geração de Calor
A maioria dos componentes eletrônicos converte energia elétrica em calor, em maior ou menor quantidade, dependendo de suas características ou regime de operação.
Se este calor não for convenientemente transferido para o meio ambiente, o componente se aquece além dos limites previstos e com isso pode "queimar".
Os radiadores ou dissipadores de calor são os elementos que ajudam a fazer esta transferência, sendo por isso, de enorme importância nas montagens eletrônicas. Vamos analisar sua função.
Quando uma corrente elétrica deve vencer uma resistência para sua circulação, ou seja, encontra uma oposição, o resultado do "esforço" de sua passagem é a produção de calor. Energia elétrica se converte em calor e isso é válido para a maioria dos componentes eletrônicos comuns.
O calor liberado neste processo tende a aquecer o componente e em consequência da diferença de temperatura que se estabelece entre ele e o meio ambiente, tem início a uma transferência de calor para esse meio ambiente, conforme mostra a figura 1.
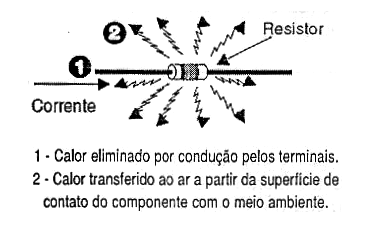
A diferença de temperatura entre o componente e o meio ambiente determina a velocidade com que o calor gerado é transferido. Assim, chega o instante em que o calor gerado e o transferido se igualam quando então a temperatura do corpo que o gera se estabiliza.
A transferência do calor gerado para o meio ambiente depende de diversos fatores como a superfície de contacto do componente com o meio ambiente, a capacidade que ele tem de conduzir o calor do ponto em que ele é gerado até o ponto de contacto com o meio ambiente e finalmente a diferença de temperatura entre esses dois pontos.
Podemos comparar a diferença de temperatura entre o ponto em que o calor é gerado (componente) e o meio ambiente (ar que o circunda) como a diferença de potencial elétrico entre os dois pontos.
O fluxo de calor entre os dois pontos é feito por um percurso de modo semelhante a uma corrente. Assim, temos um circuito "térmico" em que existe uma "resistência" que deve ser vencida pelo calor para chegar ao meio ambiente.
Se a resistência for elevada, ou seja, houver dificuldades para o calor gerado numa pastilha de um componente, por exemplo, um transistor ou um circuito integrado, chegar até o meio ambiente, sua temperatura se eleva, pois deve haver "maior tensão" para o calor sair, vencendo a oposição encontrada.
Veja que, com o aumento da "tensão" que no caso é a temperatura, temos maior "pressão" e com isso aumenta o fluxo de calor, de modo que chega um instante em que ocorre o equilíbrio da situação: a quantidade de calor gerado é igual à quantidade de calor transferido para o meio ambiente.
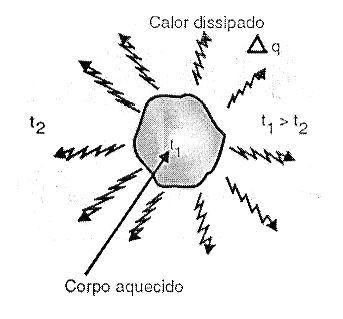
Em eletrônica, devemos cuidar para que isso ocorra numa temperatura que não comprometa a integridade do componente.
Por exemplo, o silício usado na maioria dos dispositivos semicondutores como diodos, transistores e circuitos integrados não pode se aquecer a uma temperatura maior que 125 graus centígrados, chegando em alguns casos a 150° C.
A maioria dos componentes é dotada de recursos que facilitam a condução do calor gerado para sua superfície e daí para o meio ambiente.
No entanto, muitos componentes têm dimensões insuficientes para fazer isso sozinho, ou seja, possuem uma superfície de contacto insuficiente para que o calor gerado possa ser transferido com facilidade.
Isso ocorre porque um dos fatores que influi na transferência do calor de um meio para outro é a superfície de contacto entre esses dois meios.
Transistores e circuitos integrados de potência consistem em exemplos disso.
Suas pequenas dimensões impedem que mais do que algumas centenas de miliwatts e eventualmente alguns watts de energia seja convertida em calor e transferida (dissipada) para o meio ambiente de modo eficiente.
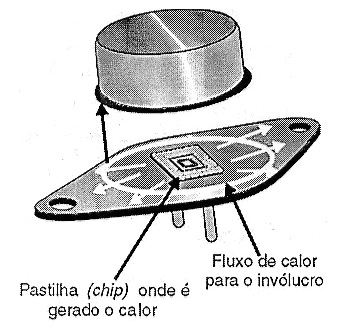
Como conseguir que estes componentes transfiram para o meio ambiente todo o calor gerado de modo que sua temperatura não se eleve além dos limites permitidos?
Levando em conta que o calor gerado pode ser transferido para o meio ambiente de três maneiras, irradiação, contacto e convecção, temos as seguintes possibilidades:
a) contacto
Os metais são bons condutores de calor. Assim, a montagem de componentes eletrônicos em contacto com superfícies maiores de metal, desde que não haja contacto elétrico, mas somente térmico, ajuda na transferência do calor.
Assim, para pequenos transistores, transistores de média potência, MOSFETs, SCRs e mesmo circuitos integrados, uma solução para o problema da transferência do calor é montá-los encostados numa superfície de metal maior, capaz de ajudar a absorver e transferir para o meio ambiente o calor gerado.
Na figura 4 temos uma solução dotada para o caso de transistores de média potência como os BD135 e TIP31 quando eles não operam com sua potência máxima.
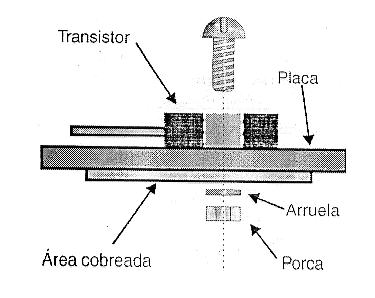
Neste caso, montamos o transistor em contacto com uma área cobreada maior da placa de circuito impresso, a qual ajuda absorver o calor gerado, e como tem uma superfície maior de contacto com o ar ela transfere esse calor para o meio ambiente.
Podemos dizer que a própria placa de circuito impresso pode ser usada como radiador de calor neste caso.
b) convecção
O componente aquecido transfere o calor para o ar ambiente que então se aquece.
O ar aquecido é mais leve que o ar frio a sua volta e por isso tende a subir. Forma-se então uma corrente de ar quente ascendente sobre o componente que "leva o calor" para cima.
Nos aparelhos de alta potência é importante deixar orifícios de ventilação para que esse ar quente seja expelido. Temos então furos por baixo por onde entra o ar frio e furos por cima por onde sai o ar quente.
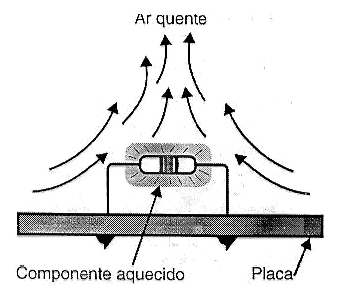
Podemos aumentar a capacidade de transferência de calor para o meio ambiente forçando a ventilação, o que pode ser feito com ajuda de um ventilador.
Este recurso é bastante usado nos equipamentos de alta potência e em fontes de alimentação de computadores, ou mesmo nos microprocessadores de computadores que possuem ventoinhas de refrigeração que forçam a circulação de ar pelos componentes que se aquecem.
Existem até "micro-ventiladores" (fan) que podem ser encaixados sobre circuitos integrados e componentes especiais para ajudar a dissipar o calor que ele gera, conforme veremos mais adiante.
c) Irradiação
Parte do calor gerado por qualquer corpo é irradiada na forma de ondas eletromagnéticas. Uma boa parte desta radiação está na faixa dos infravermelhos e para sua propagação não se necessita de um meio material.
Verifica-se que os corpos negros irradiam muito melhor o calor do que os corpos de outras cores.
Por este motivo, os componentes pintados de preto possuem uma capacidade maior de irradiação de calor do que os equivalentes que tenham invólucros de cores mais claras, conforme sugere a figura 6.
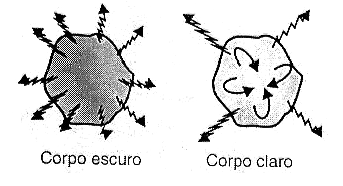
Lei de Joule
Todo dispositivo eletrônico, que não apresente uma resistência nula, gera uma certa quantidade de calor ao ser percorrido por uma corrente elétrica.
Para o caso de um resistor, a potência elétrica desenvolvida que é convertida em calor é determinada pela Lei de Joule.
O que esta lei estabelece é que a quantidade de calor gerado, ou potência dissipada (medida em watts), é proporcional ao produto da corrente pela tensão no resistor, conforme a fórmula:
P = V x I (1)
Onde:
P é a potência em watts (W)
V é a tensão em volts (V)
I é a corrente em ampères (A)
Levando em conta que pela Lei de Ohm que a corrente num resistor é proporcional à tensão em seus terminais ou R = V/I, também podemos escrever para a Lei de Joule que:
P = R x I2 (2)
P= V2/R (3)
Exemplo de cálculo:
Calcular a potência dissipada por um resistor de 10 ohms quando ligado a um gerador de 12 volts.
Resolução: como temos a tensão e a resistência, usamos a fórmula (3).
P = (12 x 12)/10
P = 144 / 10
P = 14,4 watts
Como o dispositivo de resistência nula é ideal, não existindo na prática, podemos dizer que todos os dispositivos percorridos por corrente num circuito real geram calor.
Assim, os semicondutores de potência tais como transistores bipolares, MOSFETs, IGBTs, SCRs, Triacs, etc., no estado de condução geram calor.
Como eles não são perfeitos, sempre apresentando uma certa resistência, a quantidade de calor gerado dependerá da intensidade da corrente e dessa resistência.
Como essa resistência causa uma queda de tensão no dispositivo, podemos dizer que a potência gerada é dada pelo produto dessa queda de tensão pela intensidade da corrente conduzida.
O calor gerado pelos dispositivos precisa ser dissipada para que não causem elevações de temperatura capazes de danificá-los.
Conforme estudamos nos capítulos anteriores, todos os componentes semicondutores possuem limites de dissipação e temperaturas máximas em que podem operar.
Isso significa que esses dispositivos, em condições normais de operação não conseguem dissipar o máximo de calor que o fabricante prevê para uma aplicação típica.
Nesses casos, o dispositivo deve contar com recursos adicionais para dissipar o calor gerado, ou seja, com dissipadores de calor.
O dissipador de calor
Para os casos em que o calor gerado é grande, precisando ser transferido para o meio ambiente de modo que o componente não tenha sua temperatura elevada acima dos limites que ele tolera, devem ser usados meios auxiliares.
Assim, além de recursos que permitem espalhar o calor pela própria placa de circuito impresso, através dos materiais, a ventilação forçada, o principal meio, sem dúvida é o que faz uso dos radiadores ou dissipadores de calor.
Estes elementos aproveitam todos os três modos de transferência de calor para o meio ambiente.
Assim, a quantidade de calor que um radiador de calor pode transferir para o meio ambiente depende basicamente dos seguintes fatores:
a) tamanho
Na realidade, o que deve ser levado em conta é a superfície do radiador de calor que tem contacto com o meio ambiente. Para aumentar esta superfície, os radiadores são construídos com muitas dobras ou aletas, conforme mostra a figura 7.
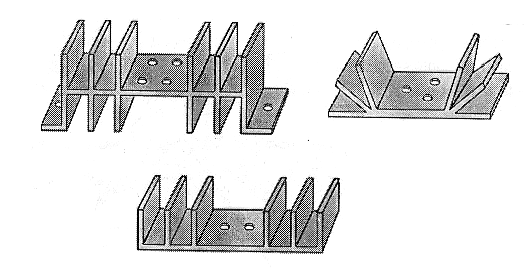
Vale então a superfície de contacto de todas as aletas com o meio ambiente.
Obtém-se assim uma superfície muito grande mesmo utilizando-se um componente que ocupa um volume relativamente pequeno, conforme damos a entender no tipo mostrado na figura 7.
Para os casos em que a potência que se deseja dissipar não seja tão grande, uma simples chapinha fixada no componente, ou ainda dobrada na forma de "U" ou "L" já pode dar resultados satisfatórios, conforme mostra a figura 8.
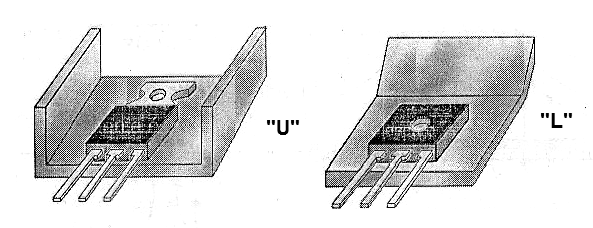
Veja que, se notarmos o aquecimento excessivo de um componente isso realmente significa que o calor produzido não está sendo transferido para o meio ambiente e isso pode não se dever exclusivamente ao radiador.
b) contacto
Deve haver um contacto físico que facilite a transferência de calor entre o componente e o radiador. De modo a melhorar este contacto, diversos são os recursos que podem ser utilizados.
Um deles consiste no uso de uma pasta térmica que é feita a base de silicone, um bom condutor de calor. Tanto o componente como o radiador são untados com esta pasta antes da montagem, conforme mostra a figura 9.
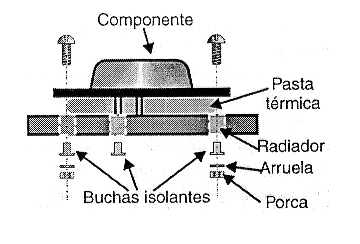
Veja que nos casos em que o componente deve ficar isolado do radiador, devemos colocar entre e ele e o radiador um elemento isolante apropriado.
Este isolador pode ser feito de mica ou um plástico especial, bom condutor de calor, mas que não conduza a corrente elétrica, conforme mostra a figura 10.
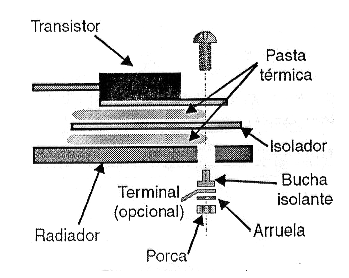
c) Irradiação
Os radiadores escuros são mais eficientes do que os claros na transferência de calor para o meio ambiente. Veja que, se a transferência por contacto já for eficiente e até houver a ajuda de ventilação, o uso de um radiador claro não altera em muito a eficiência do sistema.
Isso ocorre porque parte do calor é irradiada na forma de ondas eletromagnéticas, concentrando-se principalmente na faixa dos infravermelhos.
Parte-se das propriedades dos corpos negros que são irradiadores ideais, para se escolher materiais que possam ser usados de modo eficiente nesta forma de se livrar do calor gerado pelos componentes.
A Lei de Stefan-Boltzman mostra como a radiação produzida por um corpo negro aquecido se distribui pelo espectro.
Ventilação forçada
Também devemos lembrar os casos em que a quantidade de ar em contacto com as aletas que devem transferir o calor pode ser sensivelmente aumentada com o uso de ventilação forçada, como ocorre no caso do uso dos “fans”, muitos comuns em dispositivos que exigem uma grande taxa de transferência de calor, caso dos microprocessadores.
Na figura 11 temos um dissipador com fan ou cooler (ventoinha).
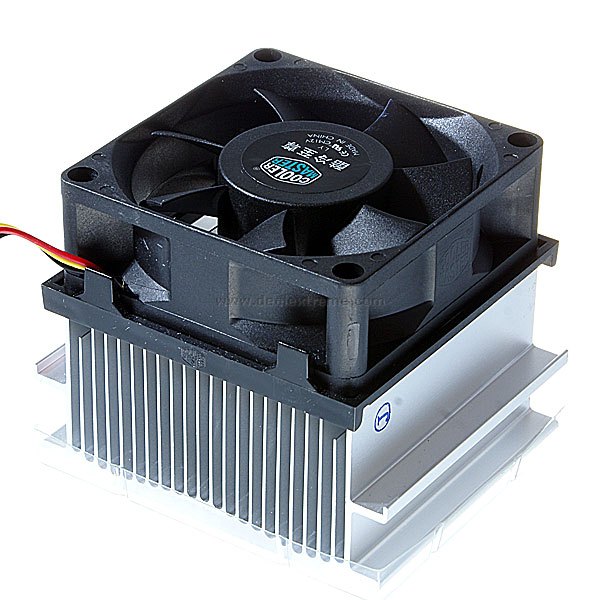
Um tipo de dissipador de calor que tem uso cada vez mais freqüente é o que emprega um dispositivo de Efeito Peltier.
Este dispositivo, mostrado na figura 12, quando alimentado por uma tensão contínua retira o calor de uma das faces e joga-o na outra que é um dissipador comum com um fan convencional.
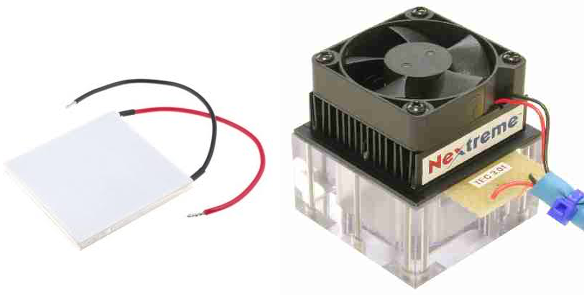
Outro tipo de dissipador com transferência forçada de calor é o que usa água ou óleo para esta finalidade. Na figura 13 temos um exemplo.
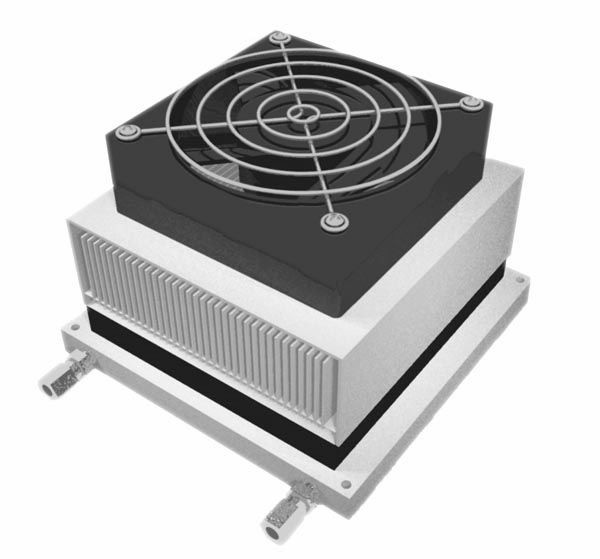
O circuito térmico
Quando acoplamos um radiador de calor a um dispositivo que gera calor, a temperatura final do dispositivo dependerá da quantidade de calor que ele gera, da velocidade com que o dispositivo pode transferir o calor gerado, e da temperatura final do ambiente para o qual o calor é transferido.
Podemos comparar isso a um “circuito térmico” em que a diferença de temperatura é a “tensão” responsável pelo fluxo de calor da fonte (componente) para o meio ambiente.
O fluxo de calor é a “corrente” e a capacidade que os diversos elementos do circuito têm de transportar esse calor é a “resistência térmica”.
Assim, conforme mostra a figura 14 podemos elaborar um “circuito térmico” que segue uma lei muito semelhante à Lei de Ohm, a tal ponto, que podemos chamá-la sem problemas de “Lei de Ohm Térmica”.
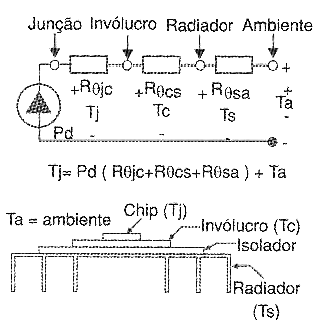
Para o desenvolvedor é preciso projetar este circuito de modo que, numa transferência normal de calor, com os recursos usados, a temperatura do componente se mantenha sempre abaixo dos máximos permitidos.
E, isso deve levar em conta que a temperatura final, que é a temperatura ambiente, pode variar entre determinados limites.
Perigos do Superaquecimento
Todos os componentes eletrônicos, capacitores, indutores, transformadores, dispositivos semicondutores, etc., possuem temperaturas máximas de operação que são especificadas pelos fabricantes.
A confiabilidade e eficiência de um componente decrescem numa taxa muito alta quando a temperatura se eleva.
Para cada 10 ou 15°C de aumento de temperatura, acima dos 50°C a taxa de falhas de um componente dobra.
Além disso, os componentes eletrônicos de comportam de maneira diferente quando a temperatura se eleva.
Os capacitores, por exemplo, passam a ter uma taxa de evaporação do eletrólito muito mais significativa o que reduz a vida útil do componente.
Componentes magnéticos apresentam perdas muito maiores quando a temperatura passa dos 100º C em muitos deles a degradação do isolamento pode ocorrer de forma acentuada.
Para os semicondutores temos diversos problemas a serem considerados quando a temperatura se eleva.
Por esse motivo é que, ao estudar diversos componentes em capítulos anteriores demos uma atenção especial à SOA (Safe Operating Area), alertando o leitor sobre os perigos de se desrespeitar seus limites
Um dos problemas que ocorre com o aquecimento, e que estudamos no caso dos diodos, é a divisão desigual das correntes e, portanto, da potência em componentes que sejam ligados em série ou em paralelo.
Esse problema pode levar a um efeito de “avalanche”, conforme mostra a figura 15, em que um dos componentes pode ser levado a um aquecimento maior irreversível até a queima.
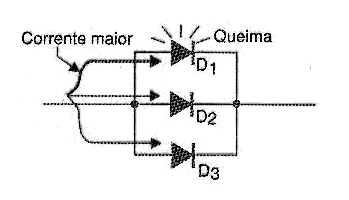
Em certos semicondutores temos ainda a redução das tensões de ruptura. A corrente de fuga aumenta e os tempos de comutação também.
Se bem que o controle das tensões e correntes nos dispositivos, o uso de componentes que sejam bem projetados no sentido de garantir excelente fluxo de calor no seu interior ajudem a minimizar os problemas de dissipação de calor, o desenvolvedor é que tem a responsabilidade de montar o componente em dissipadores eficientes quando isso se tornar necessário.
Neste caso, temos de levar em conta dois fatores:
- A montagem do dissipador em si que exige o uso de parafusos e porcas apropriados, isoladores e eventualmente graxa térmica.
- O projeto do radiador que deve não apenas ter a capacidade de dissipar o calor gerado como estar devidamente posicionado num local em que possa fazer isso de modo eficiente.
Calculando com a Resistência Térmica
Conforme vimos, o processo que vai da geração do calor pelo componente, sua transmissão através de meios apropriados até a dissipação no meio ambiente envolve um circuito térmico.
Assim, conforme mostra a figura 16, no caso de um dispositivo semicondutor temos diversas elementos neste circuito, que podem ser considerados como situados em camadas.
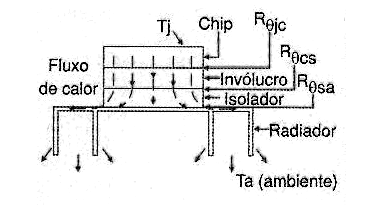
O circuito térmico equivalente para a estrutura mostrada na figura 22 é mostrado na figura17.
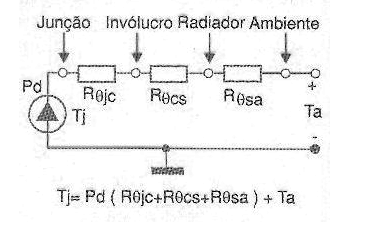
Veja que os elementos se comportam como resistores, o que quer dizer que se existirem caminhos paralelos para o fluxo de calor, eles podem ser considerados como “resistores térmicos” ligados em paralelo.
Impedância Térmica Transiente
Da mesma forma que num circuito elétrico um transiente de temperatura, ou seja, uma produção de um pico de calor pelo componente que gere um pico de calor pode causar danos ao dispositivo se não for rapidamente absorvida, impedindo que a temperatura se eleve na mesma velocidade, conforme mostra a figura 18.
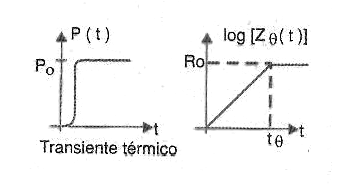
O componente térmico é equivalente a um capacitor, que absorveria um pico elétrico.
No caso do calor ele é representado pela capacidade térmica do sistema. Podemos então falar em capacidade térmica por unidade de volume:
Cv – dQ/dT (Joules/°C) que pode absorver o calor, num circuito equivalente mostrado na figura 19.
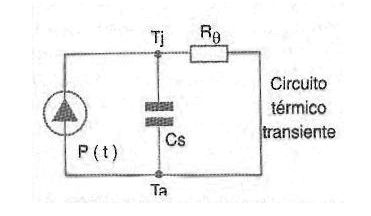
Assim, o circuito térmico equivalente será:
Cs = Cv x V
onde:
V é o volume do componente.
Chegamos então à Impedância Térmica Transiente do circuito que é dada pela fórmula junto à figura 20.
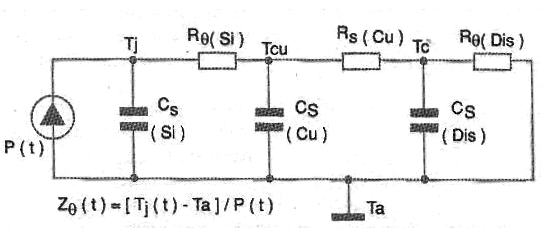
Veja que podemos falar numa constante de tempo térmico para este circuito que será dada por:
Tθ = π x Rθ x Cs / 4
Se tivermos uma estrutura multi-camadas, podemos associar às diversas capacidades térmicas de seus elementos “capacitâncias térmicas” no circuito mostrado na figura 21.
É o caso de um sistema formado por diversos tipos de materiais como o silício, cobre, e o próprio dissipador.
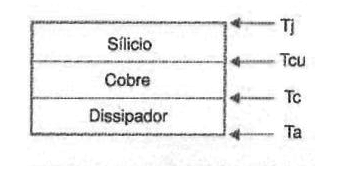
Os Dissipadores Na Prática – Como escolher
O tipo mais comum de dissipador disponível para uso em circuitos eletrônicos é o fabricado em alumínio.
Muitos possuem uma camada anodizada de óxido escuro que tem por finalidade reduzir em até 25% a resistência térmica.
Os dissipadores comuns resfriados por convecção sem ser forçada possuem uma constante de tempo térmica típica que varia entre 5 e 15 minutos. As constantes de tempo dos dissipadores com ventilação forçada são bem menores.
São os seguintes os fatores que determinam a escolha de um radiador de calor para uma determinada aplicação:
- Potência máxima que deve ser dissipada pelo componente montado no dissipador de calor. (Pdis)
- Temperatura interna máxima do componente – temperatura de junção (Tj,max)
- Resistência térmica da junção do componente para seu invólucro (Rθj)
- Temperatura ambiente máxima (Ta,max.)
A fórmula a ser aplicada será:
Rsa = (Tj,max – Ta,max) x Pdis – Rθj
Pdis e Ta,max são fixados para aplicação enquanto que Tj,max e Rθj são determinados pelo fabricante do componente.
Partindo então da idéia de que qualquer corpo que conduza e irradie calor pode funcionar como um radiador de calor podemos ter diversas técnicas para a construção de dissipadores para uso em aplicações eletrônicas.
A maioria dos tipos tem na circulação do ar a transferência da maior parte do calor gerado.
Os principais tipos, mostrados na figura 22 são:
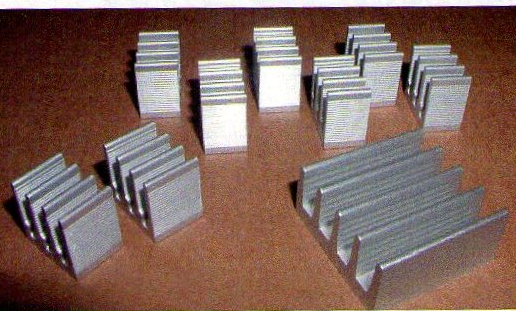
a) Estampados – são dissipadores formados por folhas de cobre ou alumínio, estampados de modo a adquirir o formato desejado. Esse tipo de dissipador é bastante usado na maioria das aplicações eletrônicas por serem baratos e por serem de fabricação fácil.
b) Por extrusão – são os mais comuns em aplicações de potência como fontes de alimentação, amplificadores, etc. O processo de extrusão facilita a obtenção de formatos bidimensionais com a capacidade de dissipar grandes quantidades de calor. Além disso, eles podem ser cortados e trabalhados de diversas maneiras. A possibilidade de se cortar aletas em corte cruzado permite a elaboração de padrões que possibilitam o aumento da performance de 10 a 20%.
c) Juntas de Tiras Pré - fabricadas – a limitação da capacidade de dissipação dos tipos que operam por convecção pode ser contornada se a superfície de contacto com o ar for aumentada. A maior exposição à corrente de ar facilita a transferência do calor gerado. Os dissipadores desse tipo são formados por aletas de alumínio coladas com epóxi a uma base fabricada por extrusão.
d) Fundidos – areia, um cerne e processo de fundição para dissipadores podem ser feitos em alumínio sem a necessidade de vácuo, cobre ou bronze. Esse tipo de dissipador tem maior desempenho em sistemas de ventilação forçada.
e) Aletas dobradas – folhas de alumínio ou cobre corrugado são usadas para aumentar a área da superfície em contacto com o ar nesse tipo de dissipador. O sistema é então fixado a uma placa que serve de base ou mesmo colado na superfície de onde o calor deve ser removido.
Como Medir a Resistência Térmica de um Dissipador
O método descrito é empírico, servindo para determinar com razoável precisão a resistência térmica de um dissipador de calor.
Tudo que o leitor precisa é de um termômetro (preferivelmente do tipo de contacto digital) e de uma fonte de calor conhecida. A fonte de calor pode ser um resistor de potência ou ainda um transistor, conforme mostra a figura 23 ligados a uma fonte ajustável de tensão.
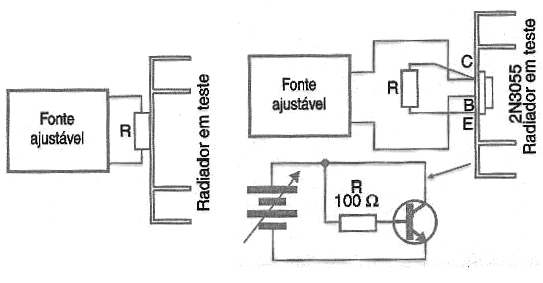
O resistor ou o transistor devem ser capazes de fornecer uma boa potência, por exemplo, o 2N3055. Será interessante que na determinação das características do dissipador, ele esteja o mais próximo possível das condições reais em que ele vai ser usado.
Por exemplo, ele já pode ser fixado na caixa do aparelho em que vai ser instalado de modo a se verificar se o sistema de ventilação é eficiente.
O que se faz então é montar o dissipador em contacto com o resistor ou transistor usado como fonte de calor. O contacto térmico perfeito é essencial para a precisão das medidas, conforme mostra a figura 24.
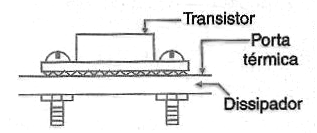
No caso de um transistor é mais fácil fazer esse contacto, pois já podemos usar pasta térmica para essa finalidade, como na montagem final do componente que vai ser utilizado.
Comece aplicando uma pequena potência ao resistor ou transistor e espere pelo menos uma hora para que ocorra o equilíbrio térmico.
Se o calor gerado for insuficiente para aquecer o dissipador (que estará ainda muito frio), aumente a potência e espere mais uma hora até a estabilização. Vá fazendo isso por etapas até obter uma temperatura final do dissipador na faixa de 50 a 60° C aproximadamente.
Anote a potência que está sendo gerada Ph multiplicando a corrente no circuito pela tensão. Anote a temperatura final medida no dissipador (th) e a temperatura ambiente (ta). Podemos então aplicar as seguintes fórmulas:
Variação da temperatura (tr)
tr = th – ta
Onde:
th – temperatura do dissipador (°C)
ta – temperatura ambiente (°C)
Potência dissipada (aplicada ao dissipador) – W
P = V x I
Onde
P – potência aplicada e dissipada em watts
V – tensão no elemento de aquecimento (V)
I – corrente no elemento de aquecimento (I)
Finalmente temos o modo de se encontrar a resistência térmica em °C/W:
Rth = Tr/P
Onde:
Rth – resistência térmica em °C/W
Tr – variação da temperatura (°C)
P – potência aplicada/dissipada (W)
Para obter maior precisão nos cálculos, o leitor pode realizar a medida várias vezes e tirar a média. Na maioria dos casos, a determinação será razoável pois os próprios fabricantes dos dissipadores especificam seus produtos com uma tolerância que chega aos 25% (para mais e para menos!).
Inércia Térmica
Como o calor gerado não é transferido para o meio ambiente imediatamente, precisando de certo tempo de “trânsito” através do dissipador, isso se traduz numa inércia térmica.
Leva tempo para o dissipador “responder” às variações de temperatura do componente nele montado.
Essa inércia deve-se basicamente à massa do dissipador, a qual deve ser aquecida, absorvendo ou cedendo calor quando a temperatura do ar ambiente ou do componente varia.
Quanto maior for um dissipador mais tempo ele demora até atingir a temperatura final de funcionamento, conforme mostra o gráfico da figura 25.
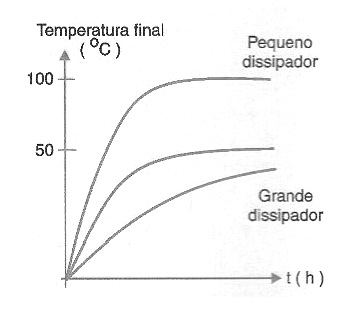
Veja então que um dissipador maior não significa necessariamente que ele pode dissipar mais calor, mas sim que ele demora mais tempo para chegar à temperatura de equilíbrio.
Uma grande inércia térmica pode ser interessante em algumas aplicações, pois ela significa a capacidade de absorver o calor gerado em transientes.
Deve-se também tomar cuidado com uma inércia excessiva, pois a temperatura do radiador pode demorar para subir atuando sobre um eventual dispositivo de proteção conectado a ele, quando a temperatura do próprio componente já atingiu um valor capaz de causar sua queima.
Montagem em Dissipadores de Calor
Na figura 26 mostramos o modo de se fazer a fixação de um componente em invólucro TO-220 (plástico) num dissipador de calor. Entre o componente e o isolador e entre o isolador e o dissipador deve ser colocada pasta térmica.
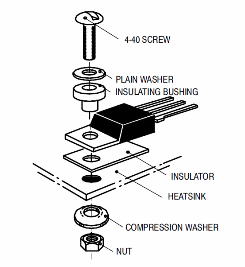
Em muitos casos, o componente não deve ter contato elétrico com o dissipador, já que o tab ou carcaça metálica normalmente possuem conexão com o coletor de transistores ou anodo de SCRs. A prova de contacto é mostrada na figura 27.
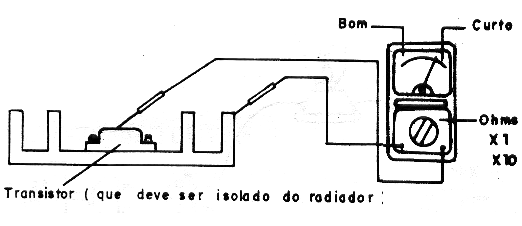
Um contato indevido (baixa resistência) pode causar curto-circuitos.
Para os circuitos integrados de potência em invólucro DIL que possuem aletas para fixação de dissipadores, do tipo aba com encaixe na placa, conforme mostra a figura 28, mostramos o procedimento para se encaixar um dissipador e soldá-lo junto com a placa.
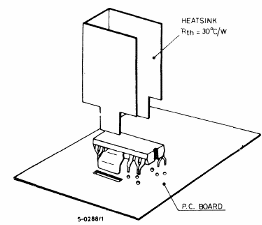
Na figura 29 temos o modo correto de se prender CIs SIL (Single in Line) em dissipadores de calor. Dependendo a aplicação pode ser usado isolador de mica ou plástico e ainda pasta térmica para ajudar na transferência do calor gerado.
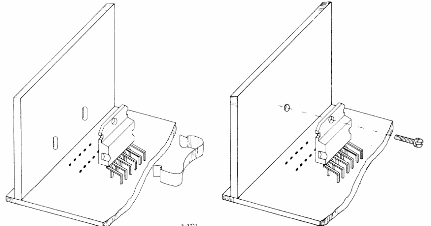